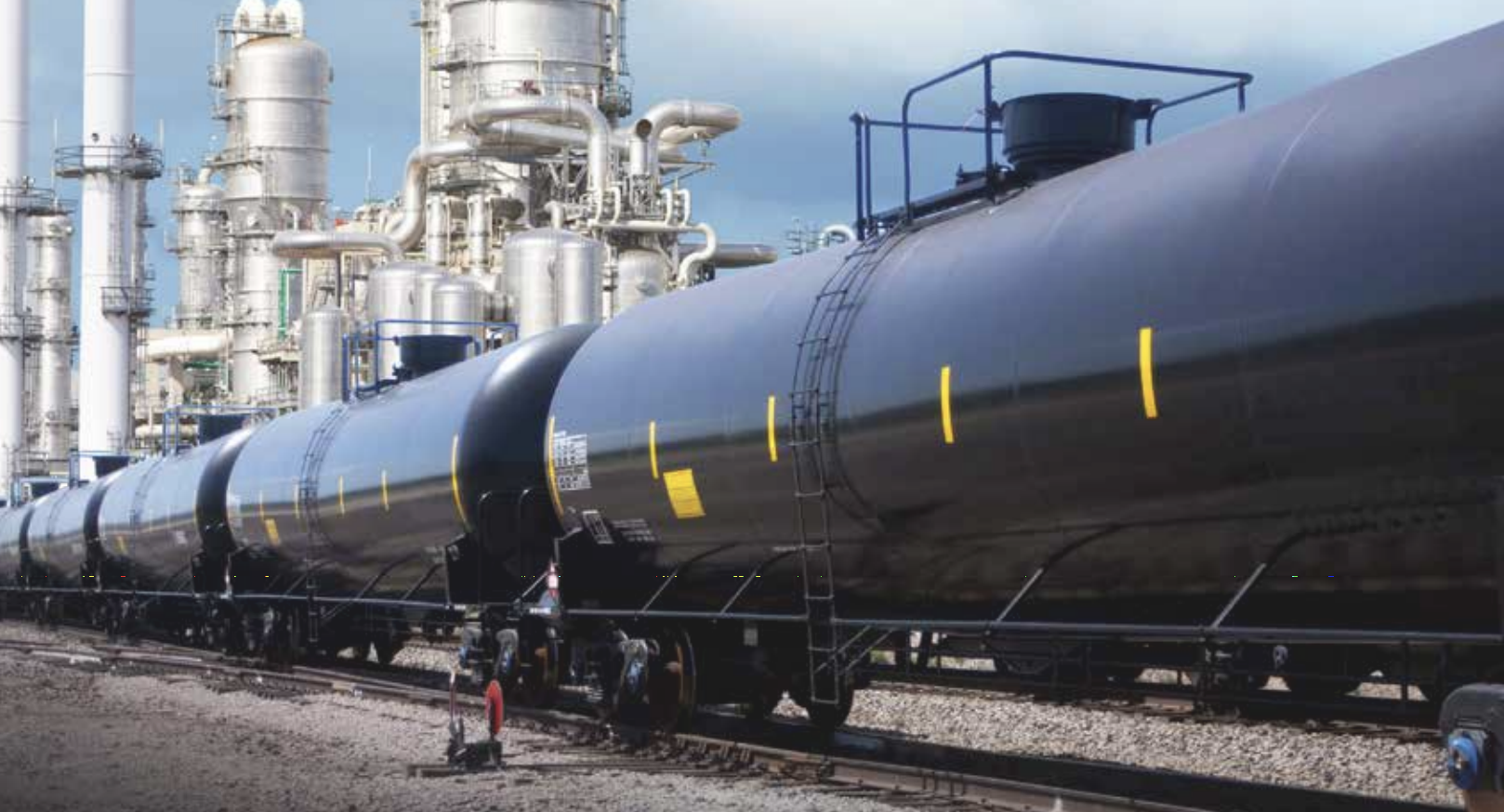
While ethylene oxide (EO) is a basic compound in many commonly used products, it can be quite volatile. This colorless gas is flammable and highly reactive, and acute exposure to EO can lead to severe health hazards. These characteristics and their potential risks to humans and the environment requires EO to be handled with the utmost care during transport, much of which is performed via pressurized railcar.
As a gas, EO is much harder to detect. That means that by the time you smell it, it may be too late. The Occupational Safety and Health Administration (OSHA) puts EO’s exposure limit at one part per one million parts of air as measured over an eight-hour time-weighted average.
Therefore, it is imperative that the equipment outfitting the railcars that transport EO possess leak-prevention capabilities, primarily at sealed areas or connection points. Recognizing the importance of controlling EO vapors and preventing their release in everyday handling activities, or during railway accidents and non-accidental release (NAR) incidents, Midland Manufacturing, Inc., has created an Ethylene Oxide Enhanced Fittings Package. This family of equipment and components has been developed with the risks associated with EO handling in mind, and their implementation can help ensure safer handling, transport and delivery of EO. The equipment options in this fittings package include:
- Low-Profile Pressure Relief Valve (PRV): Designed to extend less than three inches above the pressure plate. This reduces the chance that the PRV will be sheared off during a rollover incident. The PRV is also equipped with two protective O-rings and top/bottom stem guides, which help minimize the chance that a NAR will occur.
- Angle Valves: Midland 2” angle valves feature the lowest number of potential leak paths, which are even better assured via triple seals and bubble-testing. The elevated seat design also permits self-draining, which mitigates against the concern that product may become trapped or be released accidentally.
- Check Valves: Designed to provide flow rates up to 37,000 pounds per hour, helping prevent inadvertent damage-causing closures. Should the valve “check” because of an excess-flow condition, a built-in pressure bypass enables rapid reopening and continued operation after the cause is corrected.
To further aid the operators of railcars that transport EO, and knowing that these cars require the most reliable and up-to-date equipment, Midland has developed a Valve Remanufacturing & Repair Program, with repair/remanufacturing locations in Skokie, IL, and Houston, TX. The program not only returns a like-new valve to the operator, but also compiles a comprehensive usage history for each individual valve. This helps operators develop the best service program for their railcars, while teaming bottom-line optimization of the fleet with optimized safety and peace of mind.
For more information on Midland Manufacturing, Inc., and its complete portfolio of tank railcar products, please visit midlandmfg.com.