Three key variables should be considered before a loading arm system is designed or built into a tank terminal facility
They say that no two snowflakes are alike. That same thing can be said for terminal loading and unloading applications and systems.
Sure, all terminals serve the same basic function – commodities are brought into or transferred out of the storage facility via various forms of transportation. However, terminal operators who view their facilities only in those rudimentary terms – along with the equipment that is used to load and unload the delivery transports
– are bound to experience shortcomings in the efficiency, reliability and safety of their loading and unloading operations. In other words, there is no one-size-fits-all solution to outfitting the loading bays at a terminal facility.
In fact, there are three critical variables – product, site and transport – that must be examined and considered completely before choosing the loading arm equipment that will be used. Only when the operator truly understands all of the idiosyncrasies inherent in their loading and unloading operation will they truly be able to furnish it with a loading arm system that efficiently, reliably and safely meets the needs of the operation.
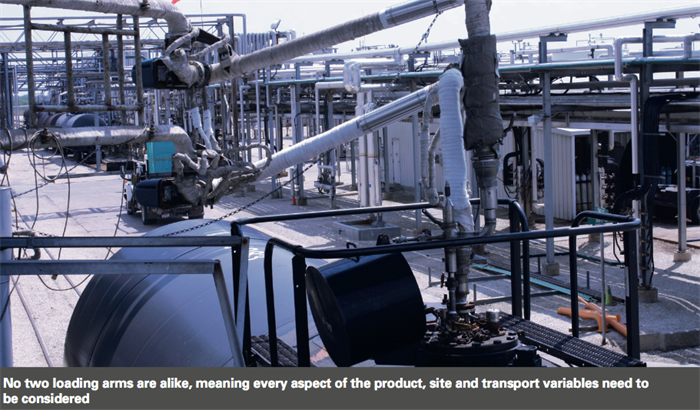
THE PRODUCT
The commodities that are stored at or transferred through a facility can vary greatly. From wastewater to corn syrup and ethanol to acids, the terminal can see it all. Again, it is the unique- ness of the commodities that are handled that requires the operator to take stock in identifying the best loading arm equipment for the operation.
Liquids with water-like viscosities will need to be handled differently than those that are thicker. Hazardous or corrosive liquids can only be transferred through equipment that features materials of construction with which they are compatible. In this instance, the operator must be aware of any safe-handling or positive material handling (PMI) certifications that must be satisfied, and if any special seal materials will be required.
Some liquids will thicken, crystallise or freeze at lower ambient temperatures; if this is the case, will the loading arms need to be equipped with steam-heated jackets or a heat-tracing system? The necessary flow rates, which, again, can be affected by liquid viscosity, will play a role in determining the size of the piping required,
as will the pressures at which the commodity is being moved.
THE SITE
When considering the acreage where the loading bays will be situated, it’s best to keep in mind the old real-estate agent’s saying: it’s all about location, location, location. Namely, the location and operational radius of the loading arms that will be installed, as well as where all of the ancillary equipment and structures will be located in relation to where the loading arms will reside.
First, the actual number of loading positions the site requires will need to be determined. Once that is established, the designer of the loading bay must work from the ground up, identifying the best place to locate the risers, which are the foundation of the loading arm system. If several loading arms are required at the bay, they must be situated in a way that the operation of one will not hinder the operation of the other arms.
A series of critical considerations is how the arm will operate, how it will be deployed, how it will store, and can it be easily and safely accessed by the operator? Again, it may be easy to envision how the system will look and work, but the single biggest mistake that terminal operators make is thinking that the arm looks great ‘in the car’, or deployed, but then can’t be maneuvered up, over or around any of a series of possible obstructions – things like piping, light poles, power lines, support columns, meters, valves, gangways, safety cages and handrails. In covered loading bays, the height of the roof will also need to be known beforehand.
Another location-related variable to consider is the actual location of the terminal, specifically where in the country it is located. As mentioned, terminals in colder climates that handle liquids that may freeze or increase in viscosity may require steam-heated jacketing or heat tracing that will keep the liquid at a temperature that allows it to flow freely. Also, special seals and materials may be needed if the system is to operate effectively at extreme temperatures.
Finally, proper structural support must be provided for the loading arm. Loading arms can be very heavy and they often require a significant amount of support to ensure smooth operation. An improperly supported arm will be difficult to maneuver, which can also create safety issues.
THE TRANSPORT
There are numerous modes of transportation and types of containers that can be loaded and unloaded at a terminal facility. Specific to the modes of transportation, the overriding consideration is just how the vehicle will be loaded and unloaded.
Bottom loading can offer numerous benefits when compared to top loading. The most obvious is increased safety for the operator, who is not required to ascend to the top of a railcar or tank truck to perform the loading/unloading process. Bottom-loading connections are also easier to make, and if the transport has several compartments, they can also be filled simultaneously, which can reduce overall loading time. Bottom loading islands are also simpler and cheaper to build than top-loading racks, which creates obvious bottom-line benefits.
From a liquid handling standpoint, bottom loading also has some advantages. First, the actual bottom loading process creates less turbulence in the tank, which reduces the chance that dangerous static electricity will be generated. Also, bottom loading reduces the amount of vapours that are produced during the loading process, with any vapours that do occur able to be fully recovered.
The operator must also consider how the loading arms will connect to the transport. The different types of connections and valves all have their own specific operational characteristics that will need to be fully considered before coming to a final decision.
That’s not to say that top loading cannot also be an efficient and cost-effective way to load and unload railcars and tank trucks. In the cases where top loading is preferred, the operator must ensure that the loading system has sufficient horizontal range so that the arms can reach the farthest compartment without needing to re-spot the vehicle. The system must also possess sufficient vertical movement and feature drop-pipe lengths that can adjust to the varying heights of the transport vehicles.
The act of top loading also requires the user to consider different types of filling styles. If open-dome loading – where the liquid enters the transport through an opening in the top of the vehicle – is used, will vapor-recovery equipment need to be installed to capture any fugitive emissions? These components can include cover plates, hatch plugs or tapered cones. As previously noted, if a submerged-fill technique is used, the drop pipe must be long enough to reach to the bottom of the transport vehicle, which will reduce the amount of turbulence that is created during the loading process.
The operator must also be aware that, depending on the design of the loading rack, there’s a chance that mis-spotting of the transport vehicle may occur. This can be problematic, especially if the loading area is designed to handle multiple railcars at once. If railcars need to be re-spotted, time is lost. To avoid this waste of time, the loading arm system should be designed so that the arms provide the flexibility to reach any cars that have not been spotted correctly.
Finally, the operator must consider a level-detection system that lets them know when the transport is full and that the loading process should cease. This is a pivotal consideration because overfills will lead to spills that can have an adverse effect on the technician and surrounding environment, to say nothing of the monetary cost that product spills can have in the form of cleanup expenses and lost revenue.
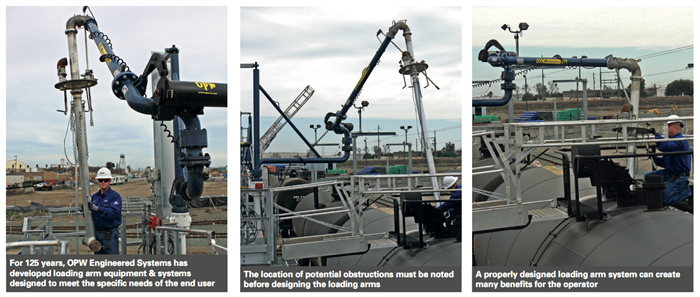
SOME FINAL CONSIDERATIONS
After satisfying the needs of the product, site and transport variables, there are several other things that need to be analysed that are specific to the actual loading arm that will be used:
• Is any special non-destructive testing (NDT) required? These tests can include radiographic (x-ray), dye-penetrant, charpy (especially for arms that will be used in cold climates) and hydrostatic testing.
• Are any special welding procedures required? For example, the handling of food-grade products and cold-weather applications may require the use of special welding processes.
• For products that need to be heated, will insulation be required? Insulation will help the liquid maintain the proper temperature while also protecting site personnel from hot piping, which is a safety concern.
• Will any additional weight be added to the arm after installation? It’s important to know this so that the proper swivel joints and counterbalance assemblies can be selected. By not using swivels and counterbalances that can handle the weight of the system the arm may become overloaded, which will decrease operational efficiency and ergonomics and create unsafe working conditions.
• Due to the design of the loading system and its method of operation, will the loading arm retain product after completing the loading operation? If not, will any special blowdown or venting connections be required?
CONCLUSION
All of these variables and considerations highlight the fact that you can’t reliably design a loading arm system in a vacuum. What looks good on paper can fail miserably in reality if the proper thought is not put into the design of the loading area and where all of its various components will be situated and how they will interact with each other.
To produce a successful installation, an ‘all of the above’ approach must be taken to the design and operation of the system. If not, the operator can expect to be ‘snowed under’ by a series of malfunctions, breakdowns, inefficiencies sand safety issues that will undoubtedly hinder the operational capabilities of the terminal, as well as its economic viability.
FOR MORE INFORMATION
This article was written by David Morrow, director of product management for OPW Engineered Systems. David.Morrow@opwglobal.com, www.opw-es.com.